96% Alumina
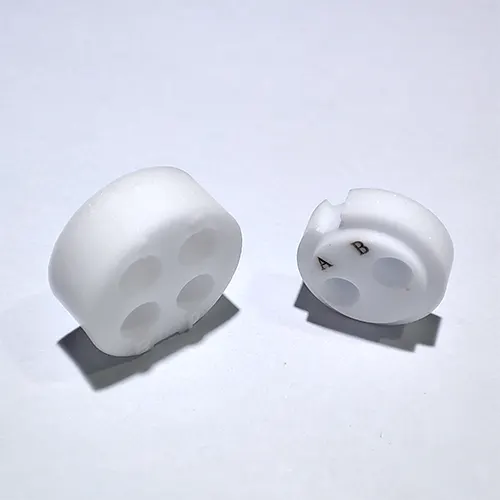
96% alumina: 96% alumina ceramics are made up of 96% alumina as the core component, optimized for performance through silicate and other additives. They have high hardness, wear resistance, and high temperature resistance (stable below 1600℃), as well as excellent chemical stability and electrical insulation properties. Its sintering process is simple and cost-effective, suitable for large-scale production. While maintaining a hardness close to high-purity alumina, its thermal shock resistance is superior to ordinary ceramics. It can be precision machined and adapted to metallization treatment, making it easy for industrial integration.
FAQ
Precision ceramics offer superior high-temperature resistance, corrosion resistance, wear resistance, and insulation, making them ideal for extreme conditions like high temperatures and high pressure. They also support higher precision processing, meeting complex design needs.
Precision ceramics are widely used in aerospace, automotive, electronics, medical, and industrial equipment industries, especially in applications requiring high performance and durability.
Precision ceramics are challenging to machine due to their high hardness and brittleness. Special equipment and processes, such as CNC machining, are required to ensure precision and surface quality.
When selecting a ceramic material, it is essential to consider specific working environments and performance requirements, such as high-temperature resistance, corrosion resistance, and mechanical strength. Different applications require ceramics with varying properties.
Precision ceramics generally have a long lifespan, with their longevity ranging from several years to even longer, depending on the usage environment (such as temperature, pressure, wear, etc.).
- PREV: Alumina
- NEXT: 99% Alumina