Silicon Nitride
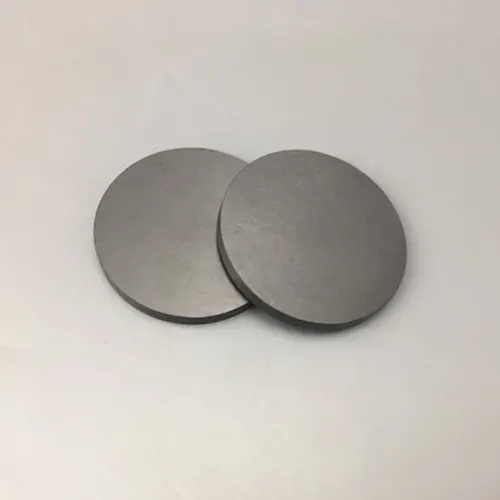
Silicon nitride, a covalent-bonded ceramic material, is known for its ultrahigh strength, extreme temperature resistance (~1900°C), low density, and exceptional chemical stability. It also features superior thermal shock resistance, preventing cracks under rapid temperature changes, along with excellent wear and oxidation resistance. These properties allow it to maintain structural integrity in harsh environments, including ultrahigh temperatures, corrosive media such as molten metals and acidic solutions, and high-speed mechanical impacts. Its durability and reliability make it indispensable for aerospace engine components, precision ceramic bearings, semiconductor etching equipment, and biomedical implants.
Recognized as a “cutting-edge structural ceramic,” silicon nitride also plays a crucial role in high-temperature industrial processes, renewable energy technologies, and advanced equipment manufacturing. Its unique combination of mechanical strength, thermal stability, and chemical resistance enables innovation across various industries, supporting the development of more efficient and durable high-performance systems.
FAQ
Precision ceramics offer superior high-temperature resistance, corrosion resistance, wear resistance, and insulation, making them ideal for extreme conditions like high temperatures and high pressure. They also support higher precision processing, meeting complex design needs.
Precision ceramics are widely used in aerospace, automotive, electronics, medical, and industrial equipment industries, especially in applications requiring high performance and durability.
Precision ceramics are challenging to machine due to their high hardness and brittleness. Special equipment and processes, such as CNC machining, are required to ensure precision and surface quality.
When selecting a ceramic material, it is essential to consider specific working environments and performance requirements, such as high-temperature resistance, corrosion resistance, and mechanical strength. Different applications require ceramics with varying properties.
Precision ceramics generally have a long lifespan, with their longevity ranging from several years to even longer, depending on the usage environment (such as temperature, pressure, wear, etc.).